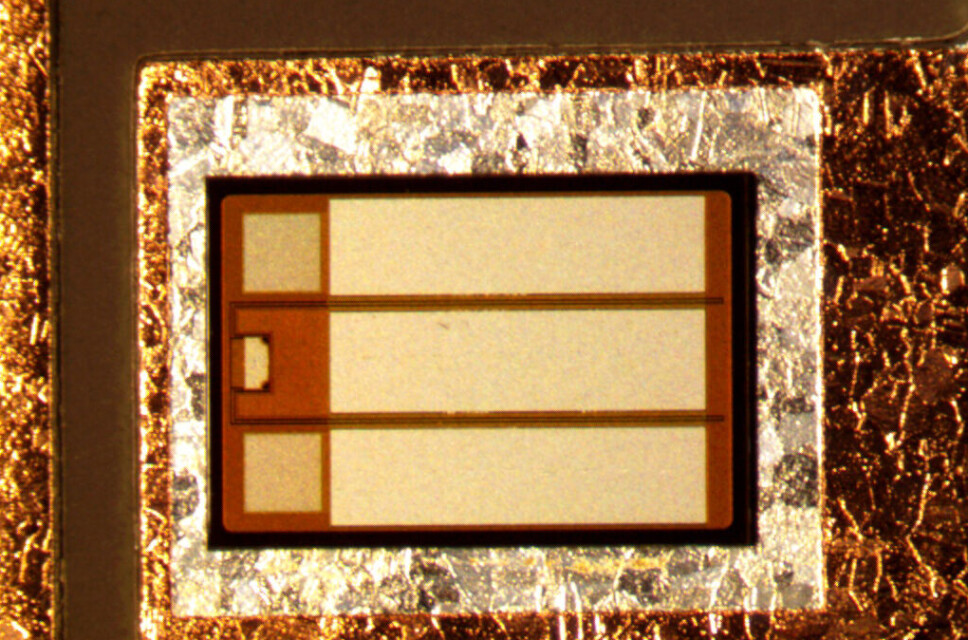
Ny monteringsmetode for SiC-brikker:
Kraftkomponenter under trykk
Denne artikkelen er 2 år eller eldre
Jim Rhodes og John Govier fra Inseto forklarer i denne artikkelen hvorfor sintring er nødvendig for å få det beste ut av silisium-karbidens elektriske og termiske egenskaper når materialet brukes i høyspente kraftmoduler.
Mange sektorer krever høyere ytelse fra høyeffekt halvledere og modulene de er innebygd i. For eksempel, innen elektromobilitet (e-mobilitet) – som inkluderer elbiler, e-sykler, e-busser og e-lastebiler – må kraftmoduler kunne svitsje høye spenninger ved høye frekvenser til laster som trekker hundrevis av ampere.
Det forventes også såkalt dyp effektsykling. For eksempel må tusenvis av maksimale akselerasjoner muliggjøres ved å kanalisere kraft fra batteripakken til elektriske motorer, samt kanalisere energi tilbake til pakken under regenerativ bremsing.
Fly og fornybar energi
Kraftmoduler spiller også en nøkkelrolle i fly- og romfartssektoren; Spesielt i de elektriske kraftsystemene (EPS) til «flere» og «alle» elektriske fly (henholdsvis MEA og AEA).
I tillegg brukes høyeffekt halvledermoduler i generering og distribusjon av elektrisitet innenfor fornybar energi, spesielt når det gjelder å få kraften som genereres av vindturbiner og solcelleceller over på det «smarte nettet».
Ulike krav
I tillegg til kravene om å svitsje mer effekt, er det også behov for høypålitelig drift i tøffe miljøer. Og, hvis du sammenligner kravene for forbruker-, industri- og bilapplikasjoner for eksempel, er det betydelige forskjeller:
- Forbrukerelektronikk er utformet for å fungere i et mildt miljø (0 til 40°C temperaturområde og lav luftfuktighet), en typisk produktlevetid på to til fem år er normalt og feilrater på opptil 10 % anses som akseptable.
- Industriell elektronikk må fungere i et relativt tøft miljø (-10 til 70°C temperaturområde og høyere luftfuktighetsnivåer), en typisk produktlevetid på fem til 10 år kreves, og feilfrekvensen bør være godt under 1 %.
- Bilelektronikk grenser nesten til kravene i den militære verden. Systemer, moduler og komponenter må (spesielt for drivverket), operere i et ekstremt tøft miljø (-40 til 160°C og 0 til 100 % fuktighet), det kreves en forventet levetid på opptil 15 år og målet er å ha 0 % feil.
Også verdt å merke seg er at bil- og romfartssektorene krever kompakte og lette formfaktorer.
Høy effekt
Fra et effektperspektiv er silisiumkarbid (SiC) dagens foretrukne halvledermateriale for bruk i kraftmoduler, som vanligvis inneholder flere metalloksid-halvlederfelt-effekttransistorer (MOSFET-er) eller isolerte gate bipolare transistorer (IGBT-er) som de viktigste kraftsvitsjingskomponentene. For eksempel er Tesla anerkjent som en av de første bilprodusentene som tok i bruk SiC-baserte kraftmoduler. Model 3 har en kraftomformer som inkluderer 24 SiC-baserte kraftmoduler fra STMicroelectronics. Hver modul har to SiC MOSFETer.
SiC for fremtiden
Den økte bruken av SiC er en viktig del av krafthalvlederindustriens veikart. For eksempel, ifølge en integrert modulprodusent (IDM), på begynnelsen av 1990-tallet ville en silisium (Si) IGBT produsert i 220 µm-prosess ha hatt en effekttetthet på rundt 30 kW/cm2. Etter hvert som IDMs fabrikasjonsgeometrier krympet, økte enhetens effekttetthet til omtrent 70 kW/cm2 på begynnelsen av 2000-tallet. I nyere tid har bytte fra Si til SiC og til en 90µm prosess gjort det mulig for IDMen å oppnå en effekttetthet på 250kW/cm2.
Varme en utfordring
Det er klart at mindre og tynnere brikkekjerner betyr en reduksjon i brikkestørrelse og kostnad, høyere effektivitet (gjennom lavere tap) og en økning i effekttetthet. Til tross for at effekttapene er lavere for SiC enn for Si, er disse imidlertid relative til den høyere effekttettheten.
Langt mer varme må ledes bort enn før, og det er en utfordring for komponentpakking.
Annen pakkemetode
Den maksimale driftstemperaturen til en standard, plastinnkapslet komponent (for eksempel i en TO 247-4 formfaktor) har en tendens til å være avhengig av pakken. Mens noen har en maksimal driftstemperatur på 175oC, er dette langt under de temperaturene som MOSFET-er og andre svitsjestrukturer som er produsert ved bruk av SiC har vist seg å fungere ved. Den maksimale driftstemperaturen er begrenset av egenskapene til plastpakken og limene eller loddemidlene i den.
For å dra mest nytte av SiCs evne til å operere ved høy temperatur, er det best å feste nakne brikker til et substrat som gir god varmespredning. En annen fordel med SiC fremfor Si er faktisk dens høye varmeledningsevne, mellom 3 og 4W/(cm2.K) sammenlignet med 1,5 4W/(cm2.K).
Metallisering
Den nakne brikken må metalliseres på baksiden før den kan plasseres. Dette har en tendens til å være en metallisering med tre metaller - ved å legge til et lag med titan, deretter nikkel, deretter sølv (eller noen ganger gull). Bondeledninger, fra toppen av brikken til modulpinner, spiller en rolle for varmespredningen. For standard elektroniske enheter med høy effekt, brukes aluminiumtråd eller -bånd. Den termiske ledningsevnen til aluminium er ca. 2,3W/(cm2.K). For SiC brukes kobber (eller kobberkledning i aluminium). Dens varmeledningsevne er omtrent 4W/(cm2.K) og dens elektriske ledningsevne er også bedre.
Et populært substrat er kobber, og for de fleste bruksområder kan brikken loddes på plass. Nok en gang flytter SiC grensense. Den termiske ledningsevnen til loddetinn er ikke så god (ca. 25W/(m.K) for blyfrie loddemidler, som SnAg og SnAgCu) og smeltepunktet er ca. 220oC.
Pressing & sintring
Et alternativ til lodding er sintring. En pasta bestående av monometalliske partikler (på mindre enn 1 µm i størrelse) og et flussmiddel trykkes, på samme måte som loddepasta påføres et kretskort, på et substrat i mønstre som tilsvarer formene og plasseringene til SiC-brikkene.
Substratet varmes opp for å fordampe flussmiddelet og brikkene plasseres. Sintringsprosessen - som ofte utføres i en inert atmosfære (eller i sjeldne tilfeller et vakuum) for å forhindre oksidasjon av metalloverflater – er en kombinasjon av varme og trykk (en nedadgående kraft på toppen av brikkene).
Høyt trykk
Trykket, som kan være opptil noen titalls MPa, tjener to formål. For det første betyr det at en lavere temperatur kan brukes til å binde materialene, samtidig som bindingene som oppnås vil kunne fungere ved en høyere temperatur i felten. For det andre reduserer det risikoen for tomrom, hvis tilstedeværelse måles som en prosentandel av brikkearealet. Selv en liten tomromsprosent kan føre til delaminering og sprekkdannelse over tid, og en delaminert brikke kan resultere i katastrofal feil på grunn av de høye strømmene som svitsjes.
Sølv
Sølv er for tiden det mest populære sintringsmaterialet. Smeltepunktet er omtrent 960°C og varmeledningsevnen til en sinterpasta er mellom 130 og 250W/(m.K). Figur 1 viser en SiC-krafthalvlederbrikke, sølvsintret til et sølvbelagt kobbersubstrat.
Pressing
De fleste sintringsverktøy bruker et enkelt, flatt stempel for å påføre kraft på toppen av brikkene. Brikketykkelsen vil imidlertid variere slik at sintermaterialet ikke vil bli komprimert i samme grad for alle brikker. Flerstempelsystemer bruker flere stempler for å påføre kraft på grupper av brikker, men problemet gjenstår fortsatt med å ta hensyn til forskjellige brikketykkelser innenfor hver gruppe. Løsningen, ifølge AMX Automatrix, er å ha et enkelt trykk for hver brikke; en løsning selskapet har implementert i sitt patenterte mikro-trykk sinter-verktøy (se figur 2).
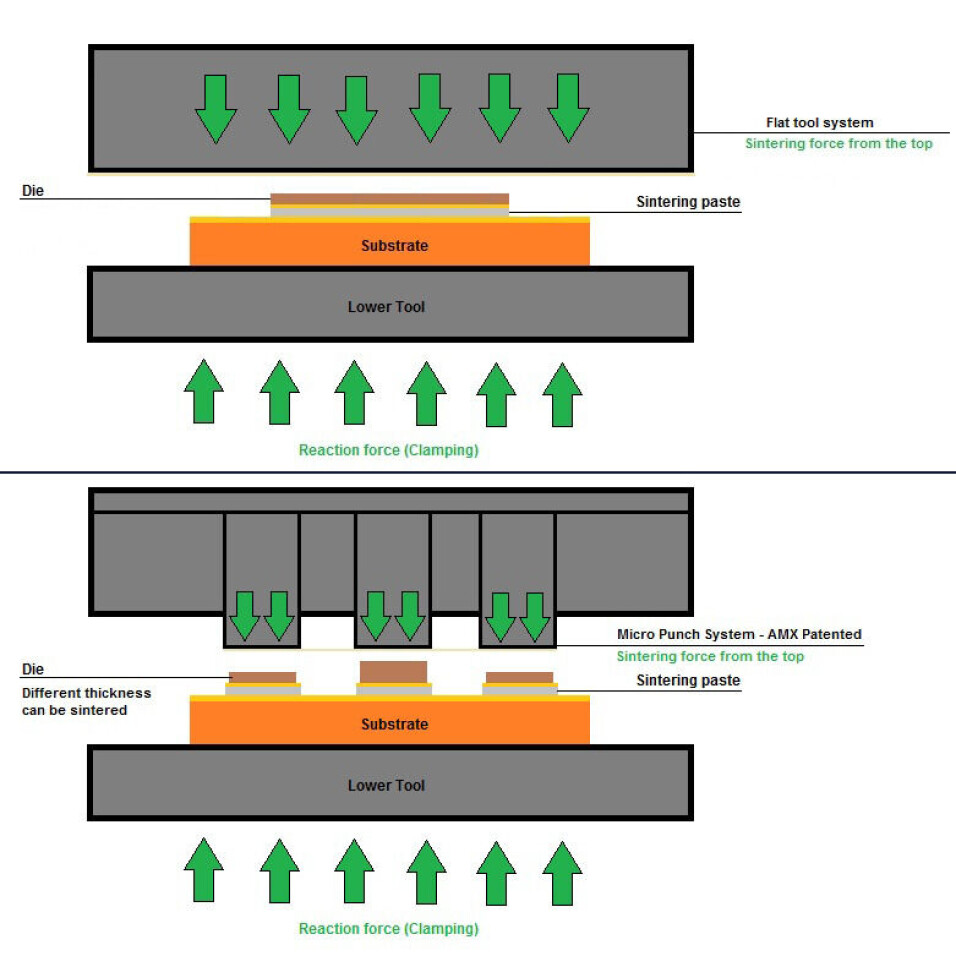
Alternative substrater
Mens de fleste sintringmetoder bruker direkte bundet kobber (DBC) eller keramiske substrater, forskes det på alternative substrater. Ifølge et foredrag som ble presentert på den 11. internasjonale konferansen om integrerte kraftelektronikksystemer (Berlin, Tyskland – mars 2020) inkluderer disse alternativene isolerte metallsubstrater (IMS), lederammer av kobber og høytemperaturstabile mønsterkort.
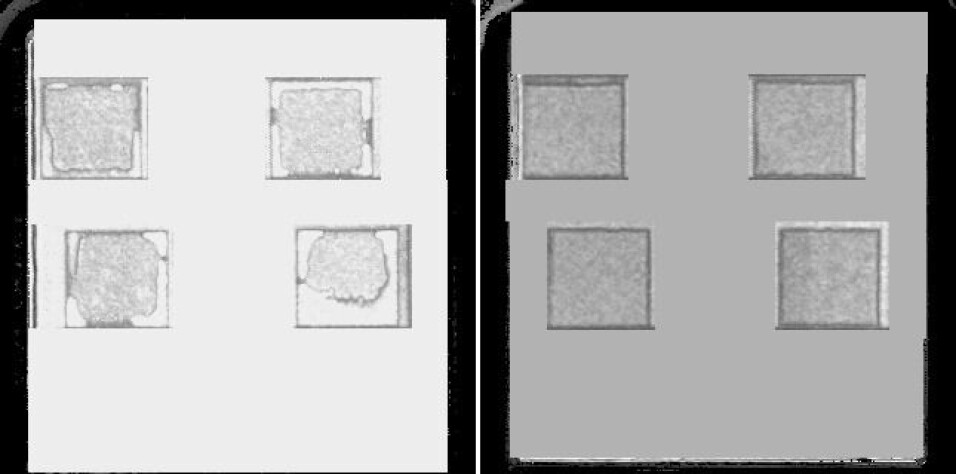
Unngå tomrom
Som nevnt, og uavhengig av underlaget som brikkene er sintret på, må kontakten mellom overflatene være så nær perfekt som mulig. Det skal ikke være tomrom. For å se etter tomrom krever imidlertid bruk av et skanningsakustisk mikroskop (SAM – se figur 3) fordi røntgenutstyr ikke fungerer – eller snarere kraften som kreves for å penetrere det metalliske underlaget er så høy at brikken blir praktisk talt usynlig.
Foretrukket prosess
Sintring er utvilsomt den foretrukne produksjonsprosessen for kraftmoduler der man bruker (og ønsker å få mest mulig ut av) SiC-brikker. Sinteren må være så fri for hulrom som mulig hvis modulen skal gi den ytelsen og langsiktige påliteligheten som kreves i sektorene nevnt i begynnelsen av denne artikkelen.
Å minimere risikoen for hulrom under flere små brikker når de sintres i et enkelt prosesstrinn krever multi-punch-verktøy, og verifisering krever bruk av SAM-teknologi.