
Nøyaktig 3D-printing gir muligheter
Plastdeler er sentralt i og rundt mange elektronikkprodukter. Riktig design, prosess og materialvalg er alfa og omega for et vellykket resultat. Det skal Miko Plast sørge for.
Denne artikkelen er 2 år eller eldre
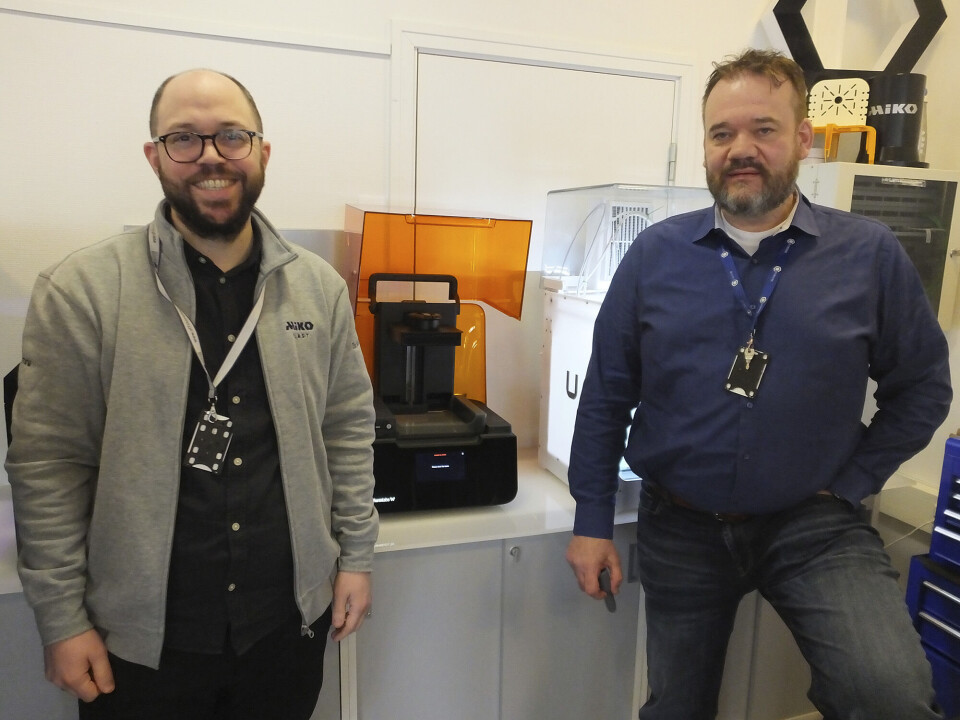
Med kunnskap om de fleste prosesser som er tilgjengelig og rundt 85.000 ulike plastmaterialer tilgjengelig , er Miko Plast AS klar for det meste som kommer av utfordringer.
Design, prosess og materiale
Et godt produkt vil alltid være resultat av god design, rett materiale og ikke minst den produksjonsprosessen som er best tilpasset anvendelse og antall. Tradisjonell sprøytestøping er imidlertid forbundet med høye kostnader til verktøybygging, og er mest egnet for produksjon i større serier.
3D-print i småserier
Ifølge Miko Plast kan imidlertid profesjonell 3D printing, eller additiv produksjon, være et alternativ i noen tilfeller. – Her kan vi levere småserier relativt raskt, og til en rimeligere pris enn sprøytestøping, forteller daglig leder Steinar Lein. – Nå kan vi lage 3D-print med svært høy nøyaktighet og gode mekaniske egenskaper, understreker han.
Smarte løsninger
Miko Plast både tegner og produserer plastdeksler og -deler i alle typer materialer, og opplever nå at elektronikkindustrien blir en stadig større kundegruppe. Blant annet har de laget innkapsling til styreelektronikken til bysykler, der de i tillegg har utviklet en metode for å enkelt «snappe» kretskortet på – og dermed slippe skruer. Det sparer kostnader, vekt og montasjetid.
Suksessprodukt
Et annet designeksempel er den elektroniske sauebjellen FindMy, som settes sammen hos Axxe og som vi tidligere har omtalt i bladet. – Dette er blitt et suksessprodukt, som nå går i 5000-serier fra oss. Det er relativt store serier i norsk sammenheng, forteller Lein. FindMy er et robust produkt som skal tåle juling, vind og vær. Selve bjellen er sprøytestøpt i glassfiberforsterket polykarbonat, og pottet (fylt) innvendig.
Navigasjonssystem
Miko Plast har videre utviklet og produsert innkapslinger til los-støttesystemet fra AD Navigasjon – som vi også har omtalt tidligere – et navigasjonssystem bestående av tre gps-enheter som plasseres på et skip sammen med en sentral på skipsbroen, for å gi losen sitt eget, pålitelige navigasjonshjelpemiddel.
Metallisert plast
– Alle kapslingene til AD Navigasjon er laget i plast. Men fordi det er krav til skjerming av elektronikken, har vi brukt en metode for å metallisere plasten innvendig – såkalt vakuum-elektrolyse, forklarer Lein. Dette er selvsagt en prosess som koster litt mer, men sparer ekstra deler, vekt og håndtering i produksjon. Her løste man også en utfordring med ønsket om et slagfast deksel i kombinasjon med en «myk» berøringsfølelse ved å støpe en del av dekslet i et mykere materiale, som samtidig fungerer som en vanntett pakning.
Alternativer til støping
Disse produktene er sprøytestøpte. Men som nevnt kan det bli en kostbar affære om ikke volumet er særlig høyt. Da finnes det imidlertid alternativer. – For lavvolum produkter har vi for eksempel tegnet kapslinger og maskinert dem ut fra halvfabrikata, forteller Lein. – Det kan typisk være nyttig i en oppstartsfase. I dag lager vi en rekke maskinerte produkter til ulike markeder, fremholder han.
Høyere kvalitet
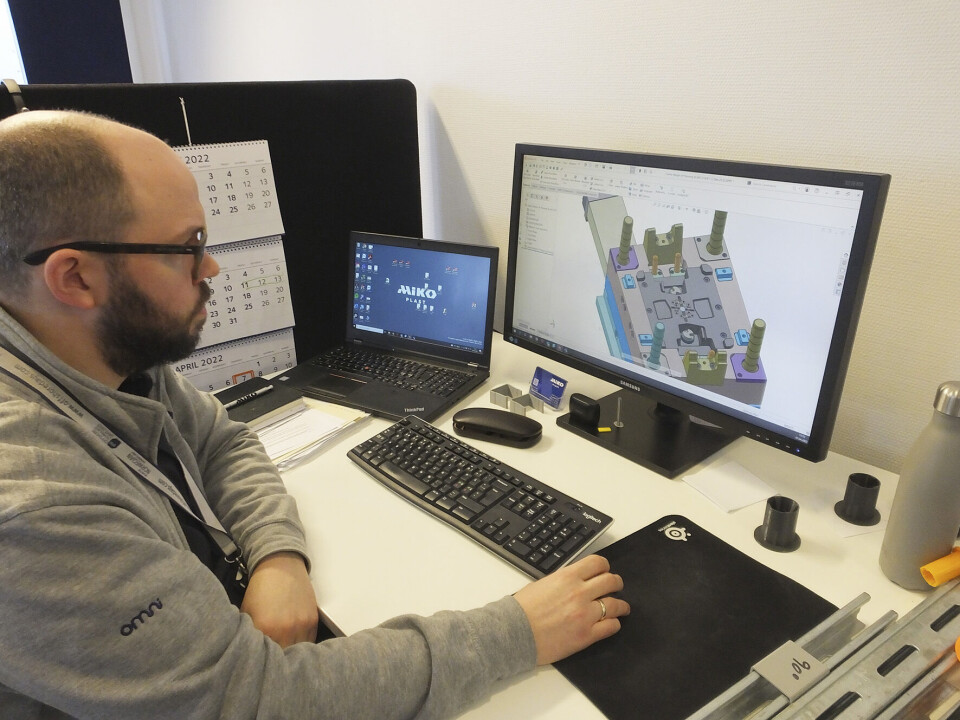
Og så har vi 3D-printing, som forlengst har passert hobbystadiet, og blitt en «moden» produksjonsteknologi. – Dette er noe vi har jobbet med i lang tid, hovedsakelig for prototyper. Men nå har vi tatt teknologien videre i produksjon av lave volumer, sier han. Miko Plast har anskaffet printere som gir høyere kvalitet og nøyaktighet, og ifølge Lein ønsker stadig flere kunder å benytte denne muligheten.
Robuste 3D-print
– Med riktige materialer og presisjon er det mulig å oppnå ekstrem styrke i disse produktene. Med såkalt SLA-print (fotokjemisk bad, red. anm.) unngår man de lagdelte og litt skjøre produktene man får med tradisjonell trådbasert 3D-print, FDM, sier Lein. I tillegg er selve materialtypene blitt flere og bedre. En stor fordel er også hurtig produksjon. – Vi kan tegne produktet på dager og produsere en serie på få uker. Det er en rask prosess, understreker han.
Raskt ute
Det gir muligheter for de som har dårlig tid, men trenger et godt nok produkt. – Dette betyr at vi kan starte produksjon straks etter at bestillingen kommer inn, sier salgsingeniør Amund Eide. – Dermed kan kunden komme raskt på markedet med nye produkter, legger han til. Senere kan kunden vurdere andre produksjonsmetoder, dersom volumet øker.
Ikke bare-bare
Selv om 3D-printing er blitt mer utbredt og kvaliteten bedre, er det ikke bare å kjøpe en 3D-printer og håpe det beste. – Du får en grei trådprinter til rundt 20.000 kroner, som kan være helt OK for å vise frem idéer og demonstrere design. Men delen du lager vil være unøyaktig, med store toleranseavvik, advarer Lein. I tillegg vil de mekaniske egenskapene være elendige sammenlignet med sprøytestøping.
Toleranser

Om man kjøper en mer avansert FDM-maskin til vil resultatet bli bedre, men fortsatt ikke godt nok. Da må man over på mer avanserte teknikker, som SLA eller SLS (selektiv lasersintring basert på pulver). Det skal til gjengjeld gi svært holdbare deler. – Dette er teknikker vi har erfaring med og teknisk kompetanse på, understreker Eide. For å eksemplifisere forskjellen i nøyaktighet på FDM- og SLA-bygde deler, så kan avviket fra spesifiserte mål være på henholdsvis 2 tideler og 2 hundredeler. I det første tilfellet kan man risikere at deler ikke passer sammen, osv.
Mekaniske egenskaper
Det har vært en voldsom utvikling på og tilgang til nye materialer, spesielt for FDM, inkludert termoplaster av lignende type som brukes i sprøytestøp. Men sluttproduktene vil uansett få ulike mekaniske egenskaper i forskjellige lengderetninger, og må designes spesifikt med tanke på dette. Innen SLA er det et mindre utvalg av materialer sammenlignet med FDM, men det øker stadig. Fortsatt er det viktig å velge materiale ut fra ønskede egenskaper/bruk, for eksempel høy stivhet eller høy bruddforlengelse.
Mer elektronikk
Hos Miko Plast merker man at elektronikkindustrien er på hugget. – Det er blitt flere oppdrag fra elektronikkindustrien i den senere tid. Ikke minst gjennom samarbeidet med OMNI alliansen, sier Lein, som også mener at det er «tiden for» den typen produkter. – Alt av nye produkter skal ha en app og en dings med elektronikk inni, avslutter han.
Miljøplast
I tillegg til å produsere «tradisjonelle» plastdeler har Miko Plast også en egen fabrikk i Enebakk, der de produserer komponenter av gjenvunnet plast.
Her produseres det dels kompenter basert på gjenvunnede råmaterialer (oppkvernet returplast), såkalt RPC, og et hybridmateriale der gjenbruksplasten er iblandet trefibre for armering. Dette materialet kalt WPC skal dermed bli både sterkere og lettere enn et rent plastprodukt, ifølge Amund Eide hos Miko Plast. – For eksempel reduserte vi vekten på et produkt fra 1,5 kg til 950 gram, sier han. – Dette er noe vi har drevet med lenge, mens først nå begynt å profilere oss skikkelig på, legger han til.